切削工具-Cutting tools-
技術論文
機械と工具2012年3月号より転載
カットピア溝入れ特殊工具
トータルコスト低減に貢献できる短納期・低価格特殊工具
1.はじめに
日本経済は今、震災・原発事故からの復旧・復興を目指しながらも電力不足への懸念、そして大幅な円高の状況下で最大の試練を迎えている。ものづくりの現場でも国際競争が激化し、更なる加工コストの低減が求められている。当社では、旋削での端面、内径溝入れ加工を得意とする『ミルコーナ』を販売しており、切屑排出性の良さ・高剛性・豊富な種類で好評を得ている(図1)。本稿ではこの『ミルコーナ』の溝入れバイトを応用し、コストダウンに成功した事例を紹介する。
2.フライス加工による端面Oリング溝(シール溝)加工用特殊工具
初めに、マシニングセンター等を使用したフライス加工による端面Oリング溝加工用特殊工具を紹介する。旋盤でのOリング溝加工は『ミルコーナ』からの選択により外径・内径・端面共に比較的簡単に加工が可能である。しかし、ワークが角物や複雑な形状である場合、あるいは大型の場合は、①専用治具の製作、②回転バランス、③設備が限定される、など課題が多い。特に小ロット品の場合これらの段取りの手間や時間を省きたいと考えるのが通常である。一方フライス加工となるとさらに加工が厄介である。フライス加工での端面Oリング溝加工はエンドミルによる加工が一般的であるが、溝巾が狭い場合などは加工条件を上げることが難しく、加工時間が大きな問題となる。さらに、Oリングのシール性を高めるためにエンドミルでの加工後に底面のカッターマーク除去に、手作業で磨き加工を行う事が多い。別の方法としては、超硬ロー付バイトやハイス完成バイトの成形品を特殊な保持具を用いての旋削方式が採られると思うが、その場合は特殊工具の製作に多大な時間と熟練作業を必要とし、結果的に非常に高価な工具となるなど課題が多い。このようなネック工程・作業をいかに効率良く行うかが各社工夫のしどころとなる。当社では、『ミルコーナ』旋削用端面溝入れ工具を応用し、特殊品ではあるが比較的簡単に対応できる、『カットピア・159Sシリーズ』を提案し、昨年名古屋で開催の展示会MECT2011に出展した。(図2)
加工する溝巾・溝深さ・溝の加工径により、インサートは『ミルコーナ』標準品をそのまま使用・もしくは標準品からの追加工とした。ホルダは特殊品としての都度対応となるが『ミルコーナ・152Sシリーズ』からの追加工又は『カットピア・159Sシリーズ』として新規製作となるが、当社の得意分野の溝入れ工具であり、比較的安価でしかも短納期での対応を可能としている。(図3)また、工具を保持する部分は九州工具製作所標準のボーリングヘッドを使用する事により、初期のセッティング及び、溝径・溝巾の微調整への対応を容易としている。(図4)溝巾4mm・深さ7.5mm溝外径φ93mmを約20秒で加工した事例がある。従来のエンドミル加工と比較すると約1/30の加工時間となり、飛躍的に速く加工することができ、大きなコストダウンとなる。(図5)さらに、加工後の底面は円周方向への旋削面となり、手作業による磨き加工は不要となる。また、高度な熟練作業を必要としない超硬スローアウェイ工具の採用で、作業の標準化と安定性を図る事が可能となった。底部コーナRの指定が有る場合は、インサートのノーズRの追加工で対応可能である。
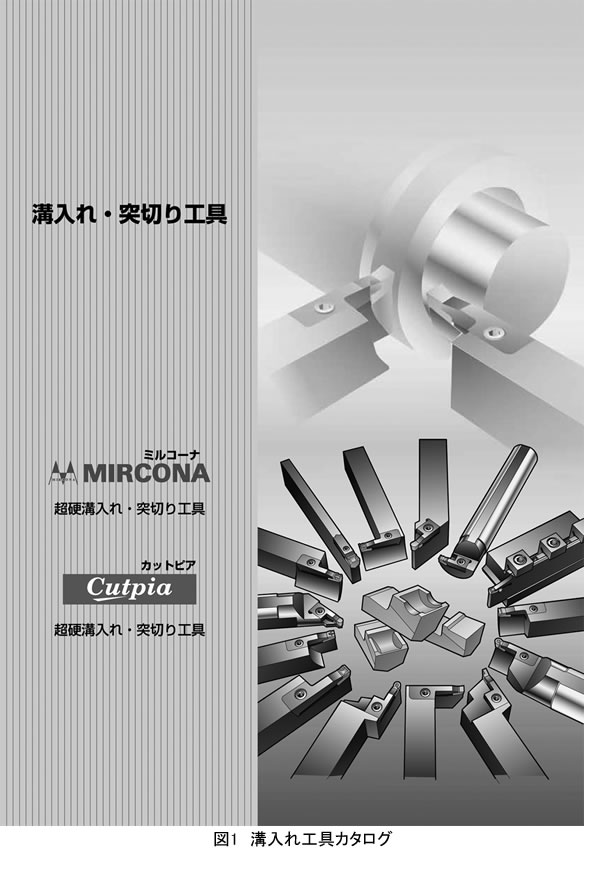
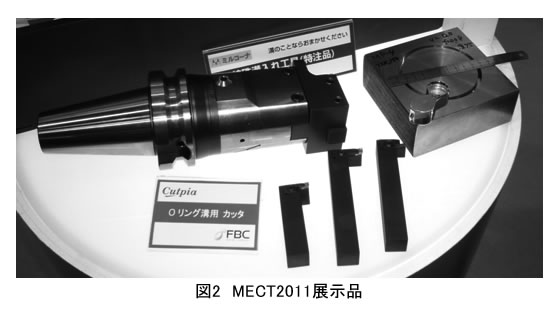
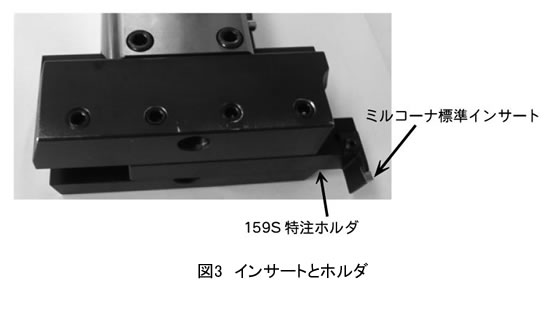
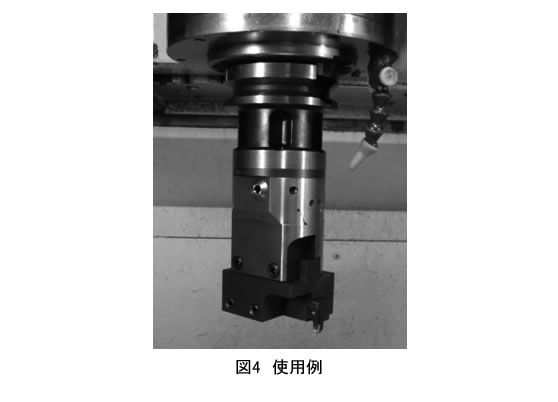
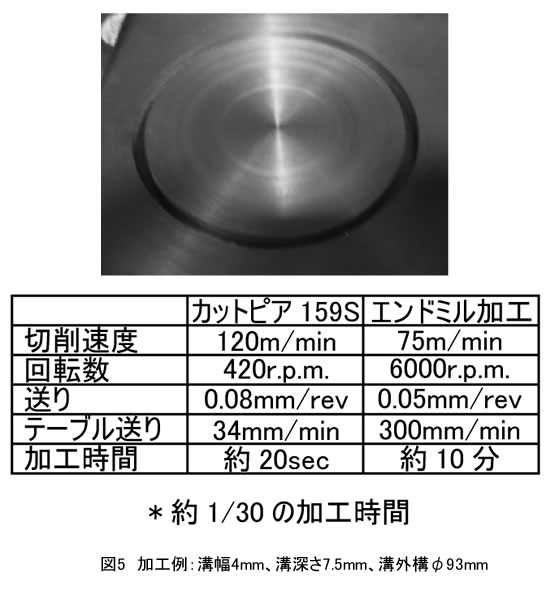
3.内径溝入れ特殊工具
溝入れの中でも内径溝入れは難しい加工でトラブルになることも多い。要因としては、切屑の排出性が悪い、切削油が届かないなどの問題が挙げられる。そして、低炭素鋼や難削材などの切屑が切れ難い材質は特に問題が起きやすい。インサート寿命の悪化、工具自体の破損、切削条件が上がらない、熱の発生などの悪影響が考えられる。これらの解決策として一般的には、①ステップを入れるなど加工プログラムによって切屑を分断する、②周速を落として加工する、③低切削抵抗のブレーカを使用する、などの対応があるが、どれも決定的とは言えない。本稿では、このようなトラブルへの対策の実例として、『内径溝入れ特注工具』について紹介する。
事例1 『カットピア・クーラントホール付旋削ホルダ』による、6-4チタンの内径溝入れ加工
本例のケースでは、外側からノズルで切削油を掛けても加工点までなかなか届き難かったため、切屑排出性の悪化と冷却不足による発熱の問題が起こっていた。6-4チタンは加工時に高熱を発するため、十分な冷却が出来ないまま周速を上げることはさらなる刃先温度の上昇につながり、工具の寿命低下となる。そのためスローアウェイ工具が使用できずシャープエッジのロー付けバイトでゆっくり切削していた。そこで当社では、ミルコーナ内径溝入れホルダにクーラントホールを追加工し、水溶性切削油を刃先のスクイ面側(ピンを立ててノズルとした)と逃げ面側の両方から吐出させ、直接加工点に掛けることを提案した。(図6)これは、当社セミドライ加工システム用として好評を得ているブルーベEBツールを応用し、クーラント仕様としたものである。クーラントホール付ホルダは他社からも類似品が出ているが、特徴としてはスクイ面側のみならず逃げ面側にもクーラントホールを設け、かつ、加工点をピンポイントで的確に狙っている点である。特に逃げ面から掛けることが非常に重要で、結果、冷却性と切屑排出性が向上した。さらに超硬スローアウェイ化に成功することで切削条件、工具寿命、作業効率を大きく改善することにつながった。
また、この『カットピア・クーラントホール付旋削ホルダ』は正面旋盤や立旋盤の大物加工にも非常に有効であり、外部給油方式と比較しても工具寿命延長・送り速度のアップ・仕上面の向上と安定性で優れ、送り速度のアップによる加工時間の大幅な短縮やコストの低減に大きく貢献できる。(図7)
『カットピア・クーラントホール付き旋削ホルダ』として様々な型番のホルダへの対応が可能であり是非ご相談頂きたい。
事例2、インサートの傾斜研磨
S25Cなどの特別な材料ではなくても、内径溝入れ加工では切屑が切れ難く大きな問題となっていた。ステップを入れても切屑が内部で詰まり、工具破損や仕上げ面が悪くなり、最悪の場合は工具の破損につながってしまう。内径溝加工で予期せぬ工具破損は、切屑が原因の場合が多い。
事例1のクーラントホール付き旋削ホルダは、放電加工で細穴を加工するため、やや高価になってしまう。そのためワンタイムの仕事(もしくは多品種)には採用し難いかもしれない。そのような場合の簡易的対策として、切屑排出性の向上を目的としてインサートのスクイ面に傾斜研磨を追加工し、成功した事例を紹介する。
ミルコーナ標準品MT-4インサートのフラットタイプのスクイ面に、切屑を手前側(出口側)にコントロールする傾斜を付けた。切屑は一箇所で絡まることなく排出され、通常のブレーカであるミルコーナ標準品MPタイプと比較しても、切削条件のアップ、仕上げ面の向上・安定につながった。しかし、溝が5mm以上の深さになると(もしくは入口からかなり深い位置に溝がある場合)効果が薄くなってしまう。そのような場合や冷却効果も求める場合には、事例1のクーラントホール付き旋削ホルダとの併用が望ましいと思われる。
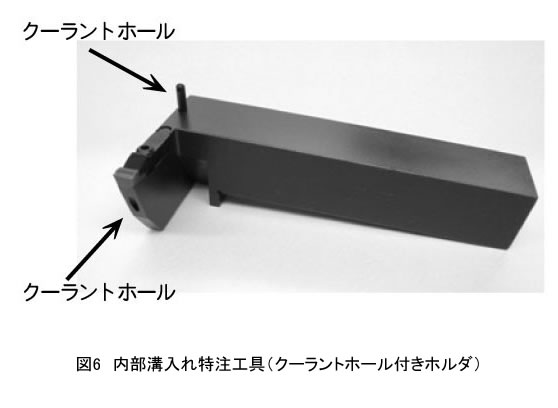
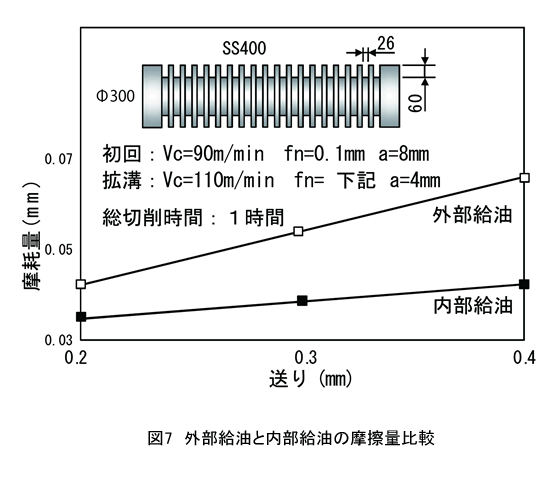
4.まとめ
特殊工具を検討の場合、価格と納期の面で採用に消極的なケースも見受けられる。しかしながら、最大の加工コスト低減は、加工時間の短縮である。本稿で紹介の実例のように標準品からの追加工や既製品に近い新規製作であれば、価格・納期でも充分満足して頂けると思う。当社営業担当へ遠慮なくご相談いただければ幸いである。